-
Shopping Bag Making Machines
-
Food Paper Bag Making Machine
-
Courier Bag Making Machine
-
Zipper Bag Making Machine
-
Diaper Bag Making Machine
-
Garbage Bag Making Machine
-
Heavy Duty Bag Making Machine
-
Liquid Bag Making Machine
-
Paper Slitting And Rewinding Machine
-
Paper Bag Handle Making Machine
-
Bag Sealing And Cutting Machine
-
Digital Bag Printing Machine
-
Bag Making Machine Parts
-
Plastic Bag Materials
-
Paper Bag Materials
Customization Color Screen Printing Machine For Nonwoven Fabric Easy To Operate
Place of Origin | Zhejiang |
---|---|
Brand Name | Xinda Pelosi |
Certification | Machinery Test Report |
Model Number | XP-LST |
Minimum Order Quantity | 1 set |
Price | To be negotiated |
Packaging Details | export standard wooden case for Automatic Roll Feeding Square Bottom Paper bag making machine |
Delivery Time | 30days |
Payment Terms | T/T, Western Union, MoneyGram |
Supply Ability | 30 Set/Sets per Year |
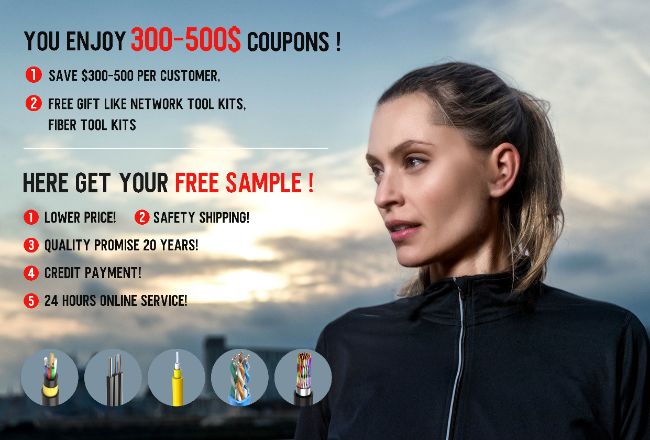
Contact me for free samples and coupons.
Whatsapp:0086 18588475571
Wechat: 0086 18588475571
Skype: sales10@aixton.com
If you have any concern, we provide 24-hour online help.
xProduct Name | Automatic Printing Machine | Usage | Non-woven Fabric Printing |
---|---|---|---|
Applicable Industries | Manufacturing Plant | Voltage | 380V |
Automatic Grade | Automatic | Dimensions(L*W*H) | 7500*1800*2200mm |
Customization | Accept | Warranty | 1 Year |
Printing Speed | 500-1400m/h | Weight | 3000 KG |
Highlight | customization color screen printing machine,customization two color non woven bag printing machine,nonwoven fabric color screen printing machine |
Easy To Operate Automatic Color Screen Printing Machine For Non-Woven Fabric Printing
Products Description
Automatic feeding, printing, drying and collecting, saving labor and overcome the constraints of weather conditions.
Pressure equalization and thick ink layer, adapt to the printing of high-grade non-woven products.
Various size of screen frame plate is available.
Multiple patterns can be printed simultaneously when do large format printing, which is largely improved the work efficiency.
Minimum effective pattern printing gap low to 10mm before and after full-pattern printing, largely reduce the material consumption.
The driving of the whole machine and chromatograph systems adopts servo motor control, ensure the printing precision.
Printing position is accurate and stable. It can be used together with transverse cutting, slitting and non-woven bag making machine, which is largely improved the production efficiency.
Specification
Model |
XDP-A1200 |
If you have different requirements, please let us know, and we will provide you with customized solutions based on the actual |
situation of the machine. |
||
|
||
|
||
|
||
|
||
|
||
|
||
Material |
Rolls of pp spunbond noven fabric |
|
Production speed |
500-1200meter/hour |
|
Fabric thickness |
45-158gsm |
|
Width of Feeding Material Roll |
1250mm |
|
Max Diameter of Material Roll |
1000mm |
|
Max Printing Size |
1300*1200mm |
|
Power supplier |
380V |
|
Total Power |
15KW/380V |
|
Overall dimension (L*W*H) |
7500*1800*2200mm |
|
Weight |
4200KG |
|
Pressure requirements: 0.8-1.0 Mpa (recommended 7.5KW screw air compressor with refrigerate air dryer and 0.6 m3air tank) |
The principle of an Automatic Color Screen Printing Machine involves the following steps:
Substrate Preparation: The substrate, such as fabric, plastic, or paper, is prepared and mounted onto the printing platform or conveyor belt of the machine.
Ink Preparation: The ink is prepared and loaded into the printing system. Different colors are typically stored in separate ink reservoirs or chambers.
Screen Preparation: Screens with stenciled designs corresponding to each color layer are set up in the printing station. Each screen represents one color in the final design.
Printing Process: The substrate moves through the printing stations, where the screens are brought into contact with the substrate surface. A squeegee blade or roller applies pressure to force ink through the open areas of the stencil onto the substrate, transferring the desired design.
Color Layering: For multicolor designs, the substrate passes through multiple printing stations, with each station applying a different color layer onto the substrate. Registration systems ensure precise alignment of each color layer to create a cohesive and accurate final design.
Drying/Curing: After printing, the substrate may pass through a drying or curing station, depending on the type of ink used. Heat, air drying, or UV curing methods are employed to dry and fix the ink onto the substrate surface, ensuring durability and color fastness.
Quality Control: Throughout the printing process, quality control measures are implemented to monitor print quality, color accuracy, and registration alignment. Any defects or inconsistencies are identified and addressed promptly to maintain printing integrity.
Finished Product: Once printing is complete and the ink is fully cured, the substrate is inspected, trimmed, and prepared for further processing or packaging. The final printed products exhibit vibrant colors, precise designs, and consistent quality, ready for distribution or use.
FAQ :
1. who are we?
We are factory ,based in Guangdong, China.
2. how can we guarantee quality?
Always a pre-production sample before mass production;
Always final Inspection before shipment;
3.what can you buy from us?
paper cup machine,nonwoven bag making machine,nonwoven printing machine,plastic bag making machine,Side Sealing machine
4. why should you buy from us not from other suppliers?
We provide high quality goods at lowest price.