-
Shopping Bag Making Machines
-
Food Paper Bag Making Machine
-
Courier Bag Making Machine
-
Zipper Bag Making Machine
-
Diaper Bag Making Machine
-
Garbage Bag Making Machine
-
Heavy Duty Bag Making Machine
-
Liquid Bag Making Machine
-
Paper Slitting And Rewinding Machine
-
Paper Bag Handle Making Machine
-
Bag Sealing And Cutting Machine
-
Digital Bag Printing Machine
-
Bag Making Machine Parts
-
Plastic Bag Materials
-
Paper Bag Materials
Motor Control High Speed Food Paper Bag Making Machine With Windows 200pcs/min
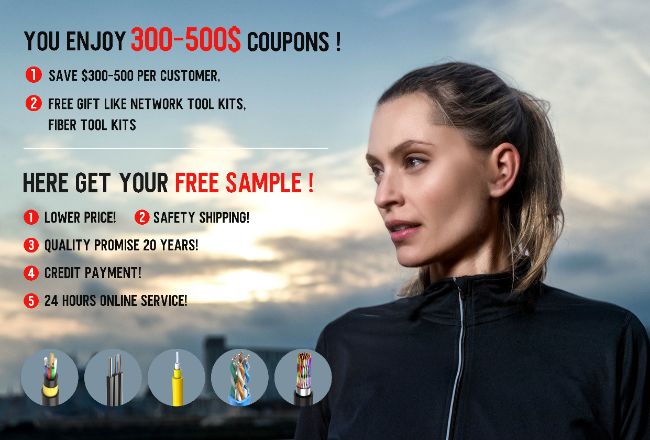
Contact me for free samples and coupons.
Whatsapp:0086 18588475571
Wechat: 0086 18588475571
Skype: sales10@aixton.com
If you have any concern, we provide 24-hour online help.
xMachine Type | Bag Forming Machine | Bag Type | Food Package Bag |
---|---|---|---|
Max Speed | 200pcs/min, 250pcs/min | Dimension(L*W*H) | 9600*2600*1900 |
Applicable Industries | Manufacturing Plant, Food & Beverage Factory, Farms, Home Use, Food Shop, Printing Shops, Food & Beverage Shops | Weight | 5600 KG |
Warranty Of Core Components | 2 Years | Voltage | 380V,3 PHASE,50/60HZ |
Paper Roll Width | 470-1050mm | Suitable Material | Low Gsm Paper |
Highlight | Motor Control Food Bag Making Machine,Motor Control Paper Bag Making Machine,Food Bag Making Machine 200pcs/min |
Manufacturing High Speed Automatic polythene plastic shopping bag making machine price
Specification :
Model
|
B220
|
B330
|
B400
|
B550
|
Paper bag length
(Cutting length) |
191-430mm
|
280-510mm
|
280-600mm
|
380-770mm
|
Paper bag width
|
80-220mm
|
150-330mm
|
150-400mm
|
220-550mm
|
Paper bag
bottom width |
50-120mm
|
70-180mm
|
90-200mm
|
100-210mm
|
Paper thickness
|
45-130g/m2
|
60-150g/m2
|
70-150g/m2
|
80-150g/m2
|
Paper roll width
|
290-710mm
|
470-1000mm
|
510-1230mm
|
630-1550mm
|
Roll paper diameter
|
1300mm
|
1300mm
|
1300mm
|
1300mm
|
Machine MAX Speed
|
250pcs/min
|
200pcs/min
|
200pcs/min
|
150pcs/min
|
Paper bag speed
|
100-200 pcs/min
|
100-160 pcs/min
|
100-160 pcs/min
|
100-150 pcs/min
|
Machine power
|
380V
3 Phase 9kw |
380V
3 Phase 11kw |
380V
3 Phase 15.5kw |
380V
3 Phase 18.8kw |
Machine weight
|
5600kg
|
8000kg
|
9000kg
|
11000kg
|
Machine size
|
8600×2600×1900 mm
|
9500×2600×1900 mm
|
10700×2600×1900 mm
|
13000×2600×2000 mm
|
Feature:
*Use PFXGP Touch Screen Human-Computer Interface, operate and control easily.
Working Process :
1. Unwinding device The unwinding device mainly consists of film coil placement frame, film coil brake, swing roller, EPC device, triangle plate superposition roller, etc., which releases the coil and folds the film with a certain tension. For tension control, the film speed is first detected by the circular encoder, the position of the swing roll is detected by the position sensor, and then the swing roll is controlled by the magnetic powder brake torque. The tension of the film is supplied by the cylinder of the swing roller, and the tension is adjusted by adjusting the pressure valve. The tension is generally set at 10~40N. The swing roller can convert the intermittent feed of bag-making into a continuous roll, and the rubber roller can only turn in the direction of the film roll to prevent backwinding when the machine is shut down.
2. Fuse sealing knife device Fuse sealing knife device includes upper and lower mechanism pressure adjustment, height adjustment, reverse device, etc. The fuse cutter transforms the rotation of the servo motor into the up and down motion of the fuse by the crank and connecting rod mechanism. The pressure adjustment of the fuse cutter is controlled by the pressure reducing valve. The pressure force of the fuse knife, that is, the "gap" can be adjusted at any time, and the hand roller rotation can be adjusted with the "gap". The temperature of the fuse knife is generally between 300 and 400 ° C, and it should be cleaned at any time.
3, bag device bag device can adjust the speed. The traction roll force of the bag can be adjusted by the pressure adjusting roller clamping force. The reduction roller slows down the bag as it passes through in order to better position the bag size on the conveyor belt. Some equipment is equipped with bag conveyors.
4, operation procedures
① Preparation: clean the guide roller, clean the foreign matter on the equipment, confirm whether the air compressor meets the requirements. Turn on the power supply, set the temperature, set the bag-making specifications.
② Connect the EPC power supply, install the film roll, and make the film penetrate to the traction roll in turn.
③ Manual control of film feed.
④ Confirm whether the fuse knife temperature reaches the set temperature, and further set various heat sealing parameters.
⑤ Adjust the folded film so that it moves along the center of the equipment, adjust the folded film of the triangle plate to the set size, and adjust the EPC device.
⑥ Adjust ultrasonic, insert, tape and other auxiliary devices and materials.
⑦ Run the equipment and adjust the position of each part.
⑧ To confirm the heat sealing strength, the setting of the fusing temperature and the bag making speed must be adjusted.
⑨ Normal production.
FQA :